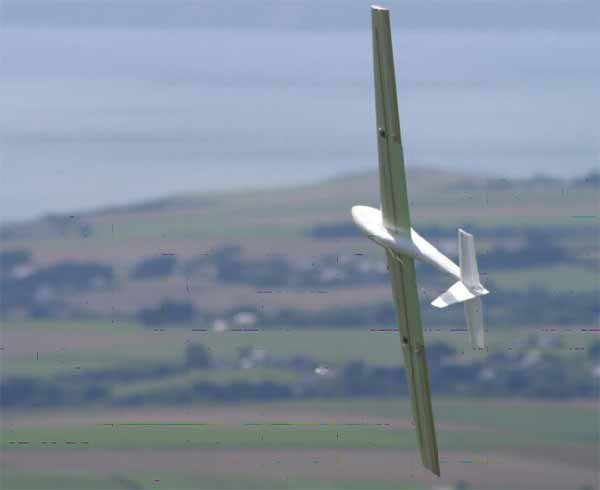
Envergure : 1800 mm
Longueur : 1000 mm
Poids : 950 gr (avec 4 x 1700 en réception !)
Ce petit dossier est fait pour vous
faire partager l’expérience de la construction d’un
planeur de voltige performant (si ! si !), comme on en
voit souvent sur les pentes bretonnes. Ces planeurs,
souvent « tout » plastique, font des figures incroyables
à quelques centimètres du sol, une dérive ou un saumon
allant même parfois taquiner le brin d’herbe qui a
pourtant bien du mal à pousser là ! La première et juste
remarque que l’on pourrait faire est « Mouais, mais t’as
vu qui pilote ??!! » Et cela est bien vrai : la voltige
débridée mentionnée ici n’est abordable que pour
certains pilotes de très haut niveau. Pour en arriver
là, ils en ont cassés, des planeurs tout beaux et tout
chers !! Et bien la formule de l' EPPonic permet à des
nigauds de mon style de se permettre, après 2-3 vols de
réglage, de faire AUSSI le zigoto au raz de la crête,
avec déclenchés par ci, tonneaux 4 facettes par là, et
le tout sans aucun stress. En effet le label « Crash
Proof » lié à la fois à la matière (EPP) et à la
conception (fixation de l’aile) est bien vérifié à
multiples reprises. Du coup, pas de stress, donc progrès
fulgurants et plaisir étonnant !!
Je remercie d’ailleurs ici Michel
et Guillaume LEROYER. Entre le père (M), fin régleur et
grand sage du Menez, et le Fils (G), pilote incroyable,
le Saint-ESPRIT ne s’est pas fait attendre pour valider
avec enthousiasme la petite machine présentée ici. Au
passage, je dirais aussi que ça en a bluffé plus d’un,
au Menez ! Na !
Remarque : les photos et
commentaires faits le long du dossier concernent la
construction du proto. La version « série » présentera
quelques différences. De même, la version finale
présentera des choix techniques différents du modèle
original (le Sonic 2m50), pour rester dans l’esprit
« Crash Proofed ». L’essentiel est de retrouver la
silhouette (mouaif …) et surtout le comportement
voltigeur (ça, c’est fait !) du « vrai » Sonic. On
trouvera en fin de dossier un tableau reprenant les
différences entre versions.
Assez de blabla …
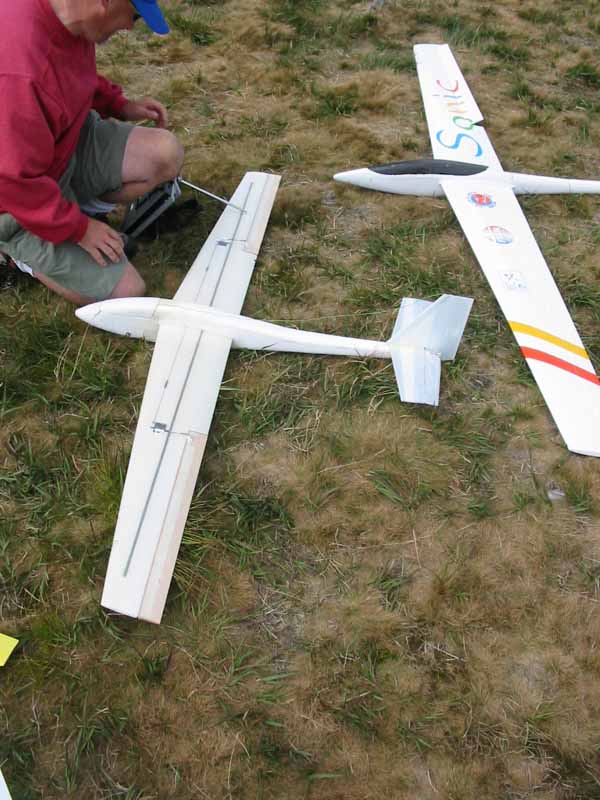
L'EPPonic à coté de la version tout fibre ....
Ce planeur est réalisé à l’aide du
logiciel et de la table de découpe CNC. De ce fait, je
joins au dossier tous les fichiers de découpes
nécessaires(.DAT et .CNC). Néanmoins, le fuselage
pourrait aussi bien être découpé à la scie à ruban,
après traçage des formes. De plus, rien n’empêche ici
d’utiliser la méthode des gabarits, également pour
l’aile. Pour cela, l’ensemble du plan est livré au
format DXF (Autocad).
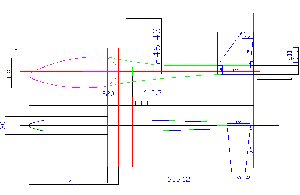
Découpe CNC classique dans de l’EPP
30 kg/m3
Voir fichiers de découpe :
Epponic_Aile.cnc
Profil empl. : SB96E.dat
Profil saum. : SB96S.dat
A noter quelques points
particuliers :
- La calage de l’aile est donné
par le vrillage positif, identique à l’empennage
comme au saumon (le V longitudinal est complété par
le calage du stab)
- Je vous conseille de laisser
la peau de –0,5 mm, ce qui permet d’éviter d’avoir
des bords de fuite en dentelle.
- L’épaisseur du bloc a une
importance capitale, dans la mesure où les
dépouilles sont réutilisées pour permettre à l’aile
de s’emboîter dans le fuseau (c’est l’une des
astuces primordiales de ce modèle : en cas de choc,
ça se déboîte tout seul, sans casse)
- Attention à prendre en compte
l’épaisseur perdue par le rayonnement. Dans le cas
du proto, le bloc faisait 35 mm, de façon a rentrer
légèrement en force dans l’ouverture de 30 mm du
fuseau (35 – 2 x rayonnement 1,2 = 32,6 mm)
Au pluriel, en effet ! Car un au
dessus, et un en dessous !
Extrados : le plus dur ici est de
trouver la position permettant d’utiliser un tube
carbone tout le long, sans le fléchir dans aucun sens.
Voici les cotes que j’ai retenues.

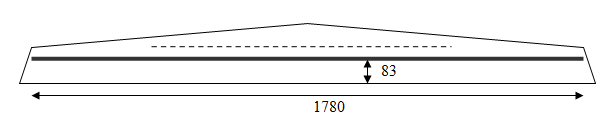
Un fraisage extrados, d’une largeur correspondant au
diamètre du tube (ici 6mm - tube cerf-volant chez Décath…),
et on colle le tube à la colle chaude (ben si ! ). Le
tube est facile à placer à l’extrados car l’extrados est
« plat » le long de l’envergure. Ceci vient de la
hauteur de réf des profils
C’est pour cela que la position du
tube n’est pas facile à trouver, et le profil au saumon
est fin !
Pour l’intrados, c’est encore moins
évident. En effet, la position des profils donne un
léger dièdre géométrique. Là, deux solutions :
Ou décider de la longueur du tube
de façon à « creuser » le moins au centre (A)
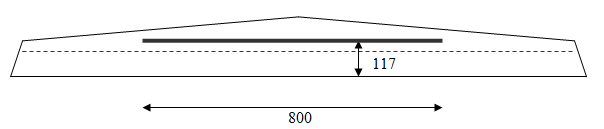
Ou chercher à mettre un longeron le
plus long possible, quelque soit la profondeur de la
saignée au centre (B). Et là, tant qu’à faire, le mieux
est de poser le longeron extrados en vis à vis de
l’intrados. (Il reste plus grand chose de mousse aux
saumons !)
Pour le proto, j’ai choisi la
solution A). Du coup, je me suis retrouvé avec un
longeron un peut court à l’intrados, mais surtout
s’arrêtant exactement au droit du début des ailerons.
Bref, une zone de rupture parfaite (mais pas encore
prouvée !!)
En cherchant bien, je suis sûr
qu’on peut trouver un compromis entre les différents
paramètres ci-dessus pour que les longerons soient le
plus « superposés » possible. Si cela est le cas, il
suffit alors de percer de part en part, à intervalles
réguliers, et de lier les deux tubes par des joncs de
carbone. La rigidité, en flexion comme ne torsion, de la
structure ainsi obtenue doit être assez étonnante !
L’autre solution pour les
longerons, qui permettrait à mon avis de les positionner
de façon parfaitement judicieuse, est la méthode de la
saignée remplie de mèche carbone. Cette méthode est
présentée parfaitement par Mister Papy Killowats dans
les dossiers du Dornier 335 et du P 38 (http://www.rc-aero.net/,
dossiers CNC). Certes plus longue et moins « simple »,
cette méthode est pour moi la meilleure pour les
prochains modèles. Ou pourquoi pas un mixte des deux (le
problème se posant toujours pour les raccords de tubes
au niveau du dièdre ou de la flèche) …. Mais en jetant
un coup d’œil sur le site du Redback (http://rc-sailplanes.dezzanet.com.au rubrique building instructions), on voit que finalement,
raccorder deux tube de carbone avec une clé en CAP n’est
pas gênant pour le poids, et reste bien plus simple
encore, car on peut prévoir la découpe des saignées
directement dans CNC. C’est en tout cas la prochaine
méthode que je testerais sur le 60-moussee !
Aussi au pluriel : il y en a
deux !!
Découper selon les cotes données :
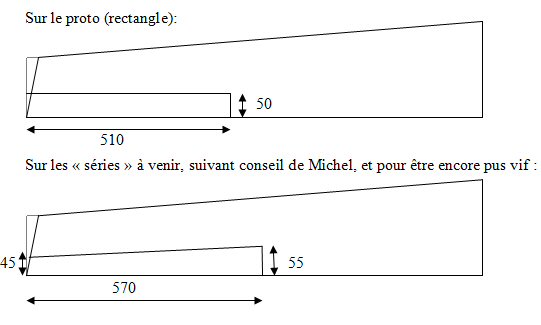
Quelque soit la version retenue, il
est indispensable de réaliser le cadre ci-dessous afin
d’obtenir la rigidité nécessaire à une réponse vive et
précise. Les profils en balsa dur du commerce ne
s’adaptent ni au profil ni à la forme des ailerons.
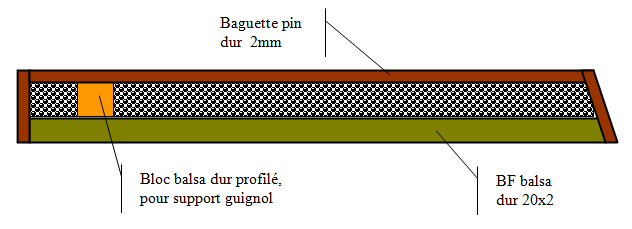
Pour aller encore plus loin, je mettrais même une
ch’tite couche de 80 gr dessus / dessous pour avoir
encore plus de répondant sur le prochain ! Et pour ne
pas me faire chier, je pourrais aussi prendre des
profils triangulaires tout faits, et les découper +
poncer !
Rien de bien compliqué : un par
aileron, câble noyé dans une saignée faite au cutter.
Les plus fins dont je dispose sont des MX3. Du fait de
la faible épaisseur du profil, je n’ai pas pu les mettre
plus loin que sur la photo, ce qui n’arrange pas le
problème éventuel de la rigidité en torsion des
ailerons (car le guignol devrait idéalement être au
moins au tiers de la longueur de l’aileron).
Alors là, rien de nouveau
Un coup de néoprène en bombe pour
encoller, et le scotch armé partout, en faisant
l’envergure d’un seul tenant. Avec du 75mm de large, je
vous promets que ça va vite ! Et puis comme ce modèle va
être « remuant », j’ai mis de l’Orastick vert en
dessous, voilà …
Pour rappel, j’entoile toujours
dans les dépouilles, pour éviter tout vrillage.
« Manchon » d’aile
En parlant des dépouilles, nous en
avons besoin maintenant, pour réaliser la partie
centrale de l’aile qui servira à l’emboîter dans le
fuseau. Je cherche encore une mot plus « aéro » que
« manchon » !!
Là encore, rien de bien compliqué.
C’est la méthode que j’avais initié avec le Sabre, mais
ce coup-ci jusqu’au bout de l’idée.
Il faut découper sur chaque
dépouille une bande de 25 mm, au niveau de l’emplanture.
On colle d’abord les deux extrados
ensemble, puis les deux intrados ensemble.
Enfin, chaque « coquille » est
collée en conséquence sur l’aile préalablement entoilée,
sans oublier bien sûr de pratiquer une ouverture pour le
passage des câbles servos. On se retrouve donc avec une
partie rectangulaire au centre de l’aile. C’est ce
« manchon » (encore ??!!) qui doit s’adapter
parfaitement avec l’ouverture du fuseau. Si vous avez
mal évalué le rayonnement et vous retrouvez avec une
épaisseur insuffisante, quelques couches de scotch armé
permettront de « rattraper » le jeu !
Il suffit de coller les deux
demi-partie entre elle.
Découper la « verrière » qui est en
fait un prétexte pour avoir accès aux servos prof et
dérive, récepteur et accus, directement monté en force
dans des logements taillés « trop petits » dans la
mousse »
Pour rigidifier le fuseau, j’ai
rajouté un tube de carbone diam 6, dans une rainure
fraisée.
J’utilise ici le principe de la Pibros en dépron, mais
en superposant du coro de 2mm.
Les cotes sont « environ »
Pour la dérive :
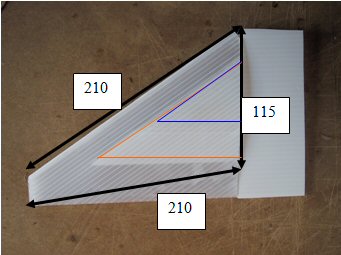
NB : les cotes ne « collent » pas avec la
photo,mais correspondent à la dérive modifiée
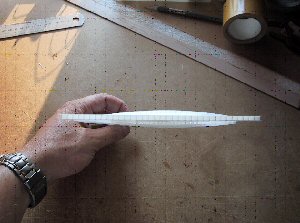
Coro 4mm au centre, 2 mm de chaque coté (petits
triangles) , extérieur en 2 mm
Pour la profondeur :
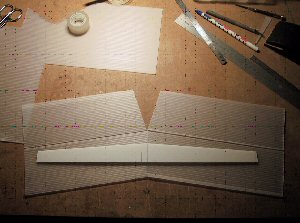
Ouvert
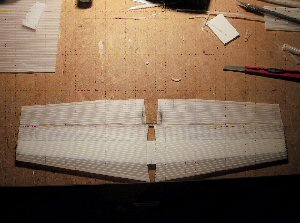
Fermé
|