- On va utiliser le
dernier morceau de la bouteille de soda.
- On a donc une bande de 19 mm de large
et d'une longueur correspondant au
périmètre de la bouteille (environs 27
cm).
- On coupe cette bande en trois pour
avoir des morceaux de 9 cm que l'on va
plier en deux bien droit, comme sur la
photo
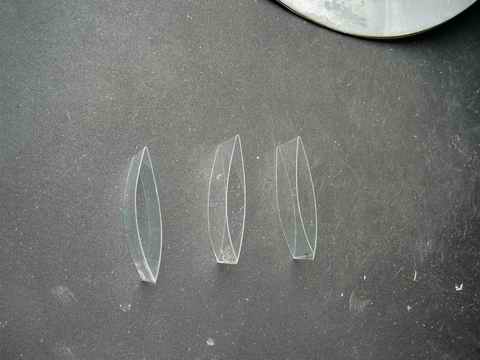
- La courbure correspond a peu près à
l'extrados de la pale, mais est dans le
mauvais sens pour l'intrados. A l'aide
d'un tournevis ou autre outil
cylindrique de petit diamètre, on va
forcer le plastique à prendre une courbe
dans l'autre sens pour correspondre à
l'intrados en roulant le plastique avec
les doigts autour de la lame du
tournevis.
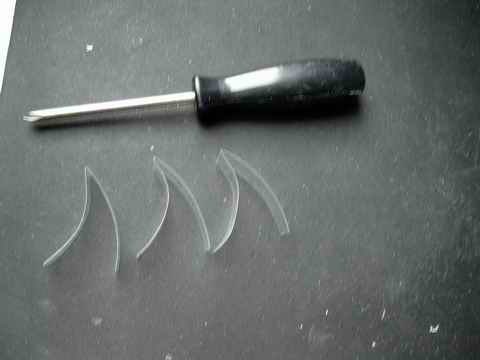
- On dispose donc de trois
pales et de leur coffrage en plastique
dur.
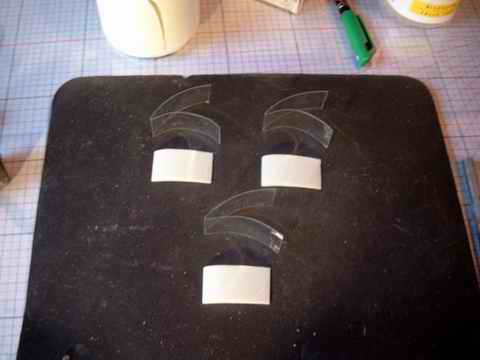
- On colle le coffrage sur chacune
des pales avec la colle universelle
(application - évaporation -serrage.)
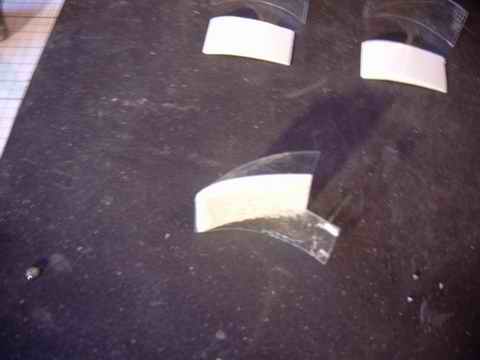
- On coupe le bord de fuite de chaque
pale, bien droit, à une longueur de 40
mm.
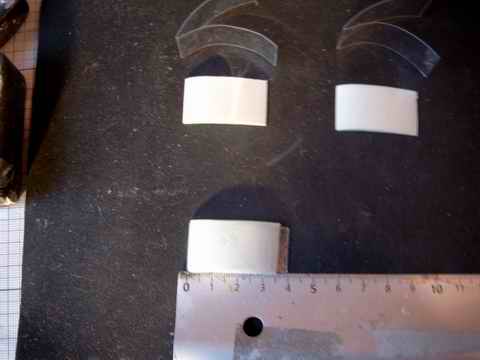
- Après séchage des pales, on les
introduit, sans forcer, dans les fentes
du tube extérieur en les passant de
l'intérieur vers l'extérieur. si ça
coince, on ajuste la découpe avec le
scalpel.
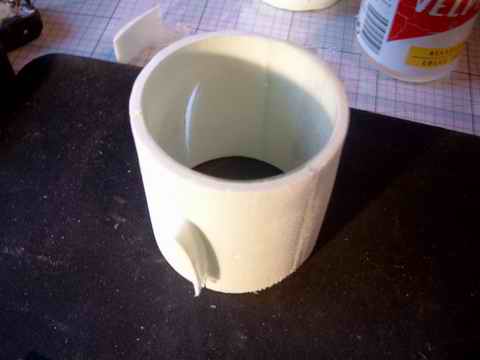
- On fait de même pour vérifier que les
pales entrent bien dans leur logement
dans le tube intérieur (de préférence en
ayant le moteur en place pour ne pas
déformer le tube) .
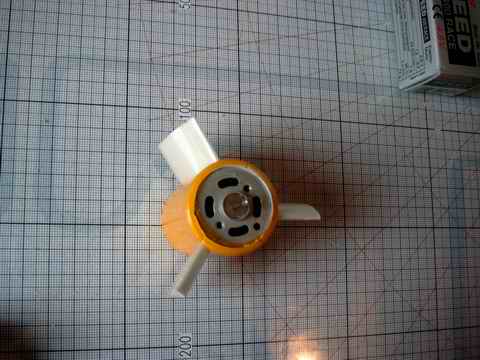
Assemblage du
corps de turbine.
- On dispose maintenant d'un tube
extérieur renforcé et découpé pour le
passage des pales, d'un tube intérieur
renforcé et découpé pour le passage des
pales et enfin de trois belles pales
renforcées. il faudra aussi préparer le
trois gabarits préparés lors du début.
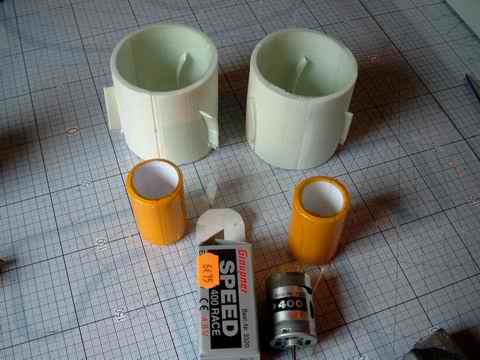
<
- On va avoir besoin d'un peu
d'époxy rapide et de quelques élastique
larges.
- On commence par coller deux
des trois pales du redresseur de flux
dans leur logement sur le tube intérieur
(équipé provisoirement du moteur). On
place la troisième pale dans son
emplacement sans la coller. On nettoie
soigneusement tous les débordements
éventuels de colle, et on place les
trois gabarits entre les pales, puis on
enserre le tout avec trois ou quatre
élastique pendant la polymérisation.
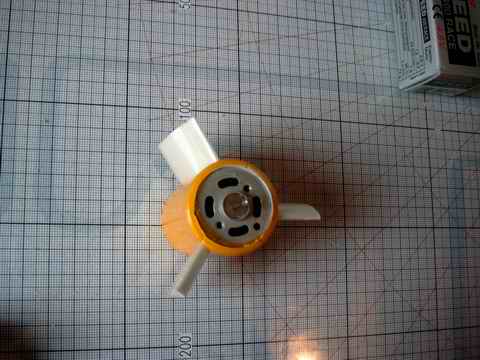
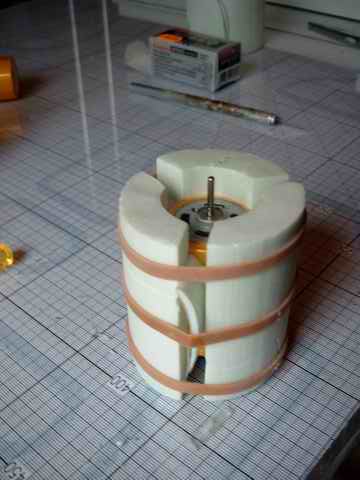
- Lorsque la colle à durci, on enlève
les élastiques et les gabarits. On fait
passer la troisième pale dans un des
emplacement du tube extérieur, et on
encolle le logement de la troisième pale
dans le tube intérieur.
- On présente le tube intérieur muni de
ses deux pales déjà collées dans le tube
extérieur et on les fait pénétrer dans
les encoches prévues. On positionne la
troisième pale en l'enfonçant jusqu'au
fond de son logement préencollé dans le
tube intérieur. On enlève rapidement les
débordements éventuels de colle et on
introduit les trois gabarits de
positionnement dans leur logement.
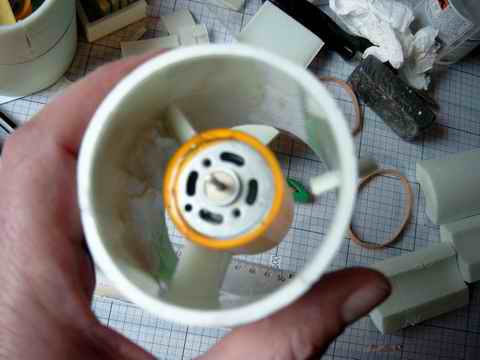
- On laisse prendre le collage de la
troisième pale dans le tube intérieur
tout en maintenant le tout en place avec
des élastiques placés autour du tube
extérieur.
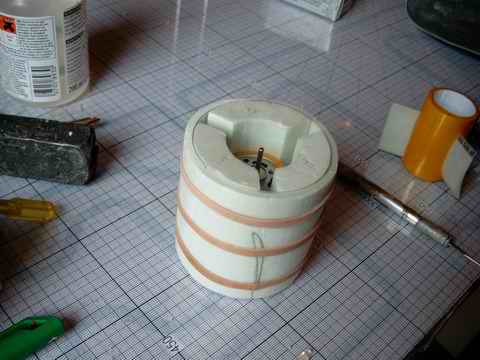
- Dès que la colle a pris, on retire les
élastique, on vérifie que les gabarits
puissent bien coulisser, on revérifie
les alignements et on bourre de l'époxy
rapide depuis l'extérieur, dans les
interstices entre le tube ext et les
pales. on laisse prendre sans bouger
avec les gabarits en place..
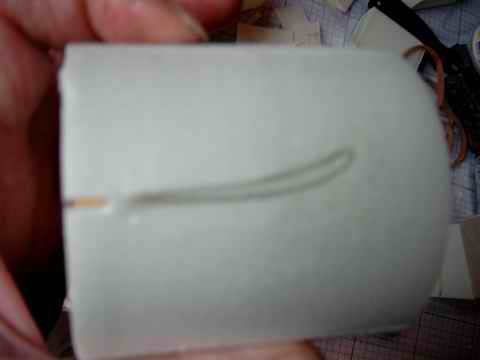
- Après durcissement complet de
l'époxy, on doit avoir un assemblage
léger et très rigide. On peut admirer la
plus grosse partie du travail terminée..
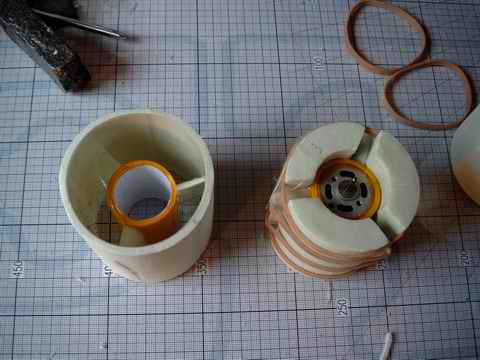
- Il faut aussi enlever tout ce qui
peut dépasser du tube extérieur(colle,
bout de pales etc) avec une lame et/ou
du papier de verre.
- Le gabarit cylindrique devrait
rentrer facilement dans l'avant
de la turbine et pouvoir tourner sans
trop de serrage.
- A ce stade, si la turbine n'est pas
prévue pour être installée dans un tube
épais comme une nacelle, on peut
renforcer le tube extérieur avec de la
fibre ou de la mèche de carbone. Pour ce
faire, on laisse le gabarit cylindrique
en place pendant le recouvrement pour
éviter tout faux rond surtout au niveau
du rotor..
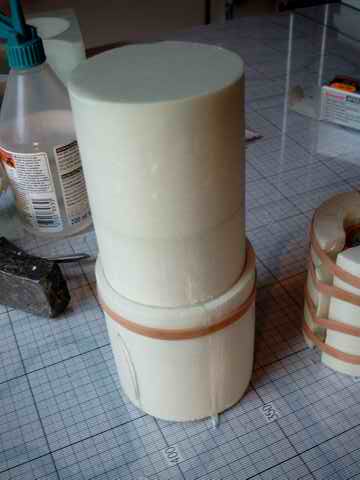
dernière minute
:
Si vous n'avez pas suivi les
discutions sur la surchauffe éventuelle
du moteur par manque d'aération, je vous
explique ici comment réaliser des
sorties d'air appelées "sorties Pierre".
Il suffit d'entailler par l'intérieur,
le tube intérieur au travers du papier,
jusqu' à la couche de plastique, sans
entamer celle ci de manière à réaliser
deux rainures d'une largeur égale aux
ouilles du moteur, sur la partie arrière
du tube, entre les ouilles et
l'extrémité arrière.
Regardez la photo si vous n'avez rien
compris!
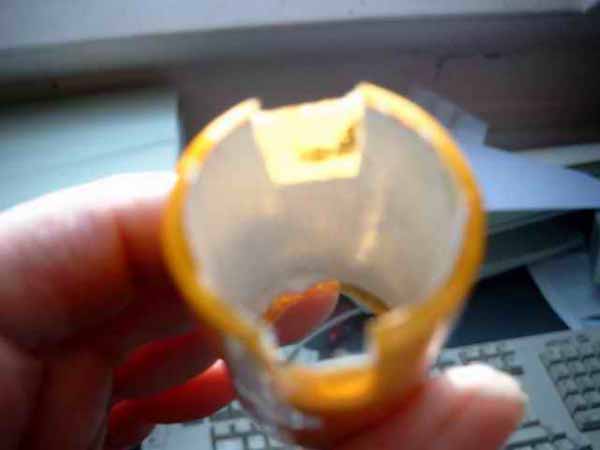
"Rotor de turbine".
Il manque la partie principale de notre
belle turbine!
- On va utiliser une "bête" hélice
GUNTHER ( 5 x 47 ) qui en dépit de ce
que certains disent, est une excellente
hélice. Ceux qui ont déjà fait la
comparaison en vol avec, par exemple,
une Graupner CAM PROP de mêmes
dimensions, beaucoup plus chère ne me
contrediront pas!
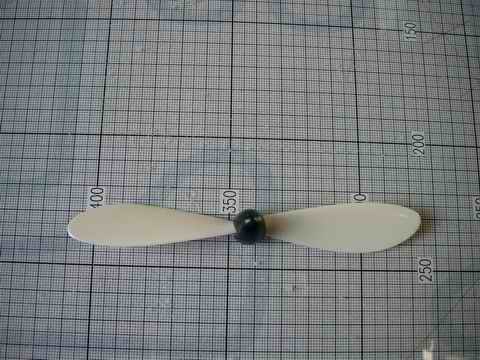
- Bon, ben cette belle hélice, on va la
massacrer (si vous pouvez en récupérer
dont les bouts de pales ont subi des
outrages.... mais vérifiez bien que au
niveau de l'axe, elle ne soit pas
fendue!)
- Première chose à faire : on prend son
pied.....à coulisse et on marque les
deux pales à 30 mm du centre en
enfonçant légèrement une des pointes à
mesurer l'intérieur dans le trou du
petit cône en plastique noir, tout en
traçant un arc de cercle sur la pale
avec l'autre pointe, comme avec un
compas.
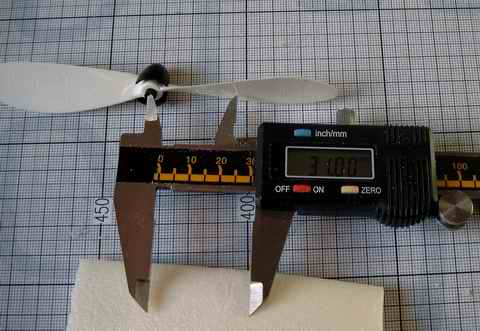
- A l'aide d'une pince coupante ou
de tout autre outil du même genre,
coupez les deux pales bien droit
,légèrement à l'extérieur du trait.
- Vous allez maintenant placer l'hélice
recoupée sur le moteur destiné à la
turbine ou un autre qui traîne dans
l'atelier,.vous allez raccorder ce
moteur à une alimentation variable, ou à
défaut un accu de faible voltage ou
encore un variateur... de façon à le
faire tourner à une vitesse raisonnable.
- Il faut aussi disposer d'une feuille
de papier de verre à gros grain. On
tient le moteur en main, bien parallèle
à la surface du papier de verre et on
approche délicatement le moignon
d'hélice en rotation de manière à
réduire légèrement son diamètre par
usure.
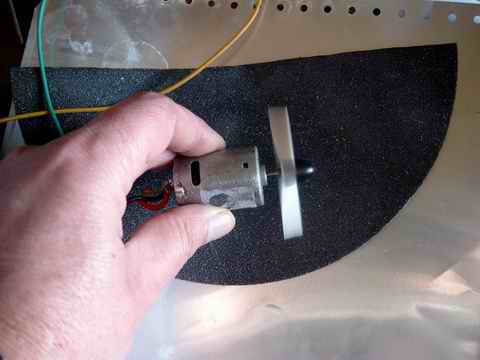
- Il faut faire cela par approches
successives en mesurant à chaque fois le
diamètre atteint avec le pied à
coulisse. Lors des dernières passes, on
contrôle moteur en place dans la
turbine que le rotor puise faire un tour
complet (à la main) en ne s'approchant
pas à moins de 0,5 mm de la paroi à
aucun endroit ( n'oublions pas que
malgré l'utilisation d'une machine
numérique, nous avons à faire à une
oeuvre artisanale et unique! donc si il
y a un léger faux rond, ce n'est pas
dramatique.
Il faut aussi tenir compte du fait que
lorsque le rotor tourne à 35000 tours,
les palles s'écartent légèrement par la
force centrifuge.

- De même, lors des essais de la
turbine, faites très très fort attention
si vous la faites tourner en la
maintenant par le carter extérieur de ne
pas écraser, même légèrement le tube
extérieur, car si une pale vient à
toucher la paroi en plastique de
bouteille, le plastique va fondre et se
boursoufler à cet endroit et vous
risquez fort de devoir tout
recommencer!!!!! Si on veut à tout prix
la faire tourner en mains, il faut soit
l'avoir déjà installé dans une nacelle
rigide, soit la maintenir au niveau des
pales du redresseur de flux sans
appuyer, et accélérer le moteur
progressivement, ce qui n'est pas
évident, vu la traction non négligeable
de l'engin.
DONC PRUDENCE !!!!!!!
Une nacelle
universelle et quelques extra....
D'abord , une petite astuce :
Les petits cônes en plastique des
hélices Gunther sont bien joli et
pratiques, mais comme j'ai déjà perdu
pas mal d'hélices de ce type en vol, je
me méfie. On peur utiliser un adaptateur
d'hélice du commerce, mais je pense
qu'ils ont tous un diamètre de 5mm alors
que le trou de l'hélice gunther fait 4mm
et qu'il ne reste pas trop de matière
autour! On peut toujours les re- forer,
mais...
J'avais déjà expliqué dans un dossier
précédant, comment je réalisais mes
adaptateurs M4 moi même. Depuis, j'en
réalise toujours mais encore plus
simplement :
Il faut une vis M4x10 de préférence à
tête hexagonale, une mèche de 6 ou une
mèche à centrer et une mèche de 2,3mm .
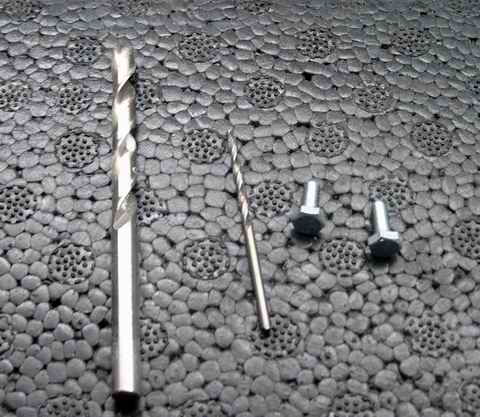
Au moyen d'une perceuse à colonne, on
fait un avant trou de centrage dans la
tête de la manière suivante : on place
une mèche de 6 ou une mèche à centrer à
l'envers dans le mandrin. On abaisse le
mandrin avec la mèche jusque dans l'étau
ajustable et on serre la queue de la
mèche dans l'étau après l'avoir bien
positionné. On pointe la tête de la vis.

Ensuite, on fait de
même avec la mèche de 2,3mm et on
traverse la vis de part en part. si la
mèche émerge bien au centre de la pointe
de la vis, on a gagné.
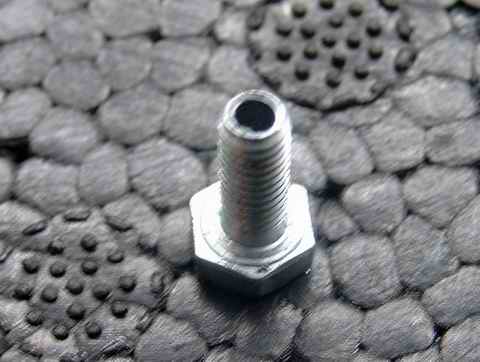
Si on à bien refroidi la mèche pendant
le forage, il faudra presser la vis sur
l'axe du moteur au moyen d'un étau..
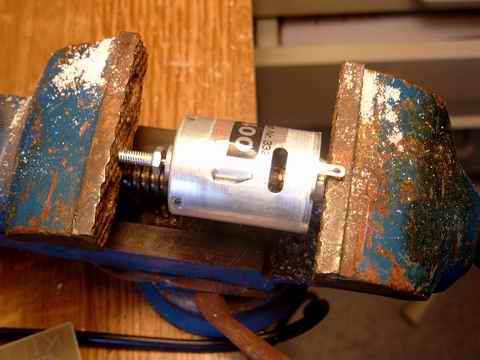
Encore une chose : pour effectuer
toutes les opérations au cours de la
réalisation de cette turbine,
spécialement lors des réglages de la
longueur des pales, il est plus commode
d'avoir un porte hélice à vis que de
devoir placer et retirer plusieurs fois
le l'hélice avec son cône en plastique à
serrage.
Mise en place de la turbine dans le
modèle :
Si la turbine est destinée à être placée
dans un fuseau, il faudra lui adjoindre
un tube d'entrée et une tuyère de
sortie.
Pour la fixation de turbine elle même,
je conseille de découper deux bagues (ou
quatre demi bagues si on veut pouvoir
ouvrir le fuseau à cet endroit), de 5 à
10 mm d'épaisseur, ayant un diamètre
intérieur correspondant au diamètre
extérieur de la turbine et une forme
extérieure correspondant à la forme
intérieure du fuseau à cet endroit.
La nacelle :
Elle est constituée de 4 pièces: la
lèvre d'entrée, la section centrale et
la "tuyere en deux parties. On
construire cette nacelle de manière à ce
qu'elle reste démontable, ce que je vais
faire, pour pouvoir faire des
modifications éventuelles à la turbine
(moteur speed 300 ou cdrom).
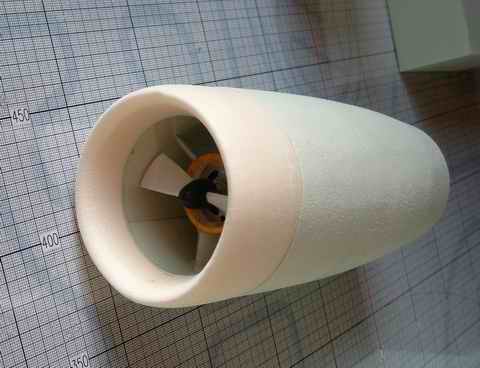
La lèvre d'entrée : notre belle machine
à découper au fil chaud est incapable de
découper des formes non développables.
On pourrait donc découper un tube épais
puis par ponçage, arriver à la forme
définitive. j'ai déjà fait ce genre de
chose, et ce n'est pas facile d'avoir un
beau travail régulier sur toute la
circonférence!
J'ai donc utilisé une astuce : j'ai
dessiné le profil de la lèvre, pour en
faire un .dat. je découpe un long
tronçon avec ce profil, mais pour une
fois, j'ai choisi le sens du poly le
plus malléable dans la longueur.
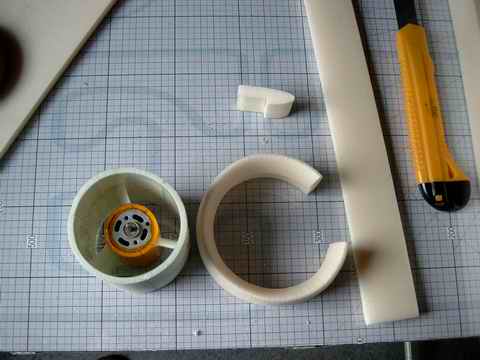
fichier
o-lèvre.cnc
Ensuite, il suffit de coller une bande
de scotch sur tout l'extérieur et de
cintrer la forme sur un mandrin d'un
diamètre plus faible que celui de la
turbine. Ensuite inl faudra mettre le
"boudin" en place sur la turbine et
couper les deux extrémités (petit à
petit) de manière a fermer le cercle
sans jeux.
On colle les deux extrémités ensemble en
dehors de la turbine et on laisse sécher
en maintenant avec un tour de scotch.
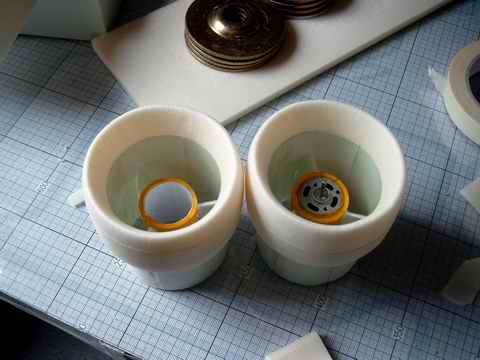
On découpe les
tronçons suivants dans du poly de 50mm
d'épaisseur placé debout. au moyen des
fichiers
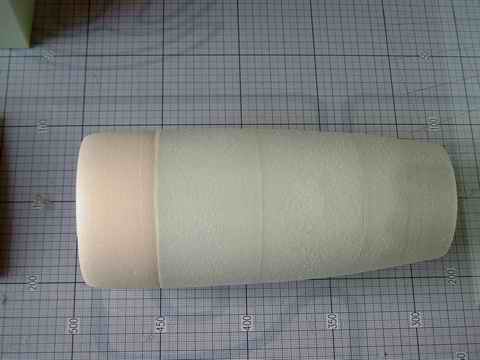
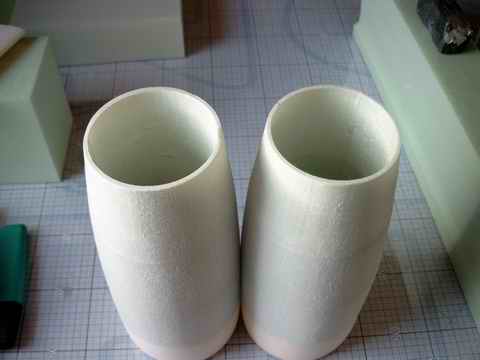
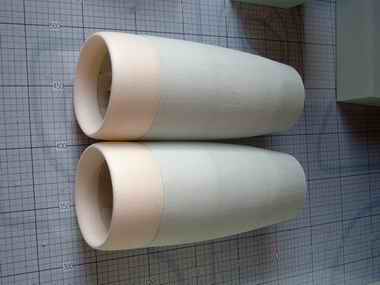